Our History
Tasmanian Forestry Industry
When Europeans first arrived to Tasmania in 1803, dense rainforests covered much of north-west Tasmania. What seemed like an unending sea of forest was looked at as a hindrance to progress, and the development of the colony. Initially product sourced from the forests included shingles, split posts, rails, palings and pit sawn lumber for the construction of buildings and farms. While ringbarking was initially used to clear forest, as the colony grew, logging for timber became an increasing activity. Ex-convicts from Launceston, employed as bark strippers, undertook the first logging activities in the north-west of Tasmania. However, as the Victorian Gold Rush hit its straps in the 1850s, demand for timber grew – and the rate of timber cutting in Tasmania rapidly increased, with the North-West a focal region, due its proximity to harbours and mainland markets. It was during this boom that mechanised sawmilling technology was introduced, increasing the rate at which millers were able to mill their cut. By the 1860s, cutting of rainforest timbers also became a focus, especially Blackwood, focussed as an export to Melbourne for furniture production. Timber cutting in circular head was established in the 1880s, when a mill was established at Smithton to exploit the stands of virgin swamp blackwood, which previously had been ringbarked and burnt by agricultural settlers intent on establishing pasture land. The success of the first sawmill, encouraged other farmers to take up timber felling. A.E. Hilder at Upper Natone operated one such mill from 1880 until its closure in the mid-1900s . From the early 1900s onward Glasgow Engineering were busy with the Tasmanian forestry industry, in particular with the manufacture of high quality logging shoes and log spikes, steam haulers, engines and boilers and saw milling plant and equipment. Testament to the quality of our log shoes was the fact that the Hardware Company of Australia based in South Melbourne would purchase log shoes in large quantities and ship them in from Tasmania. The company would even get Glasgow Engineering to manufacture special one off shoes that their customers would require from time to time. Local customers would also travel from around the state to purchase a Glasgow log shoe, in fact the shoes were so good that Salisbury Foundry organised, through a third party, the purchase of a shoe so they could take a casting from it. This was however unsuccessful and customers continued to purchase the Glasgow log shoe. The manufacture of the shoe its self was quite an art being hand forged in the smithing shop by the blacksmith and his striker. Len Jackson the blacksmith at Glasgow Engineering at the time would point with a stick for the Striker, usually an apprentice with a maul that he could hardly lift, to where he would like the ensuing blow. However if a miss strike occurred, that is, if the apprentice missed the plate and hit the blacksmiths anvil, this would usually land the poor apprentice with a smack in the teeth. No doubt an apprentice at Glasgow Engineering soon learnt how to swing a hammer correctly and accurately.
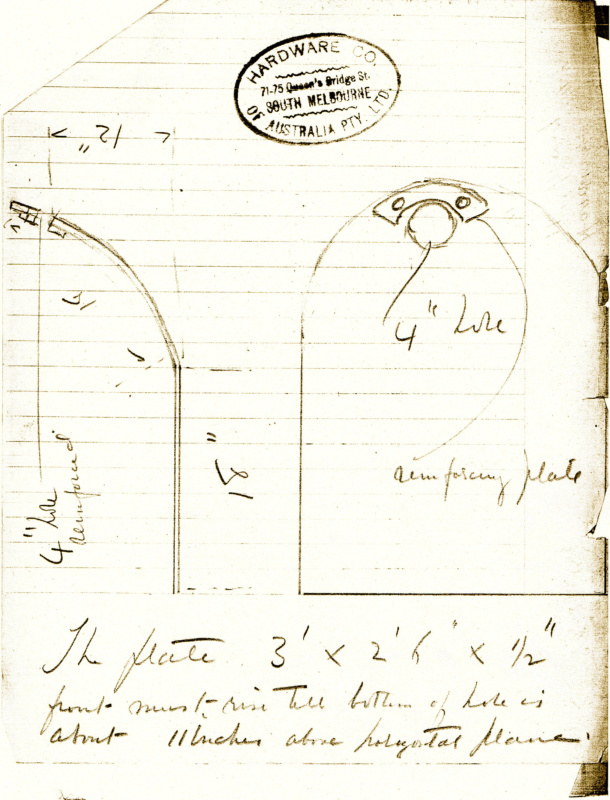
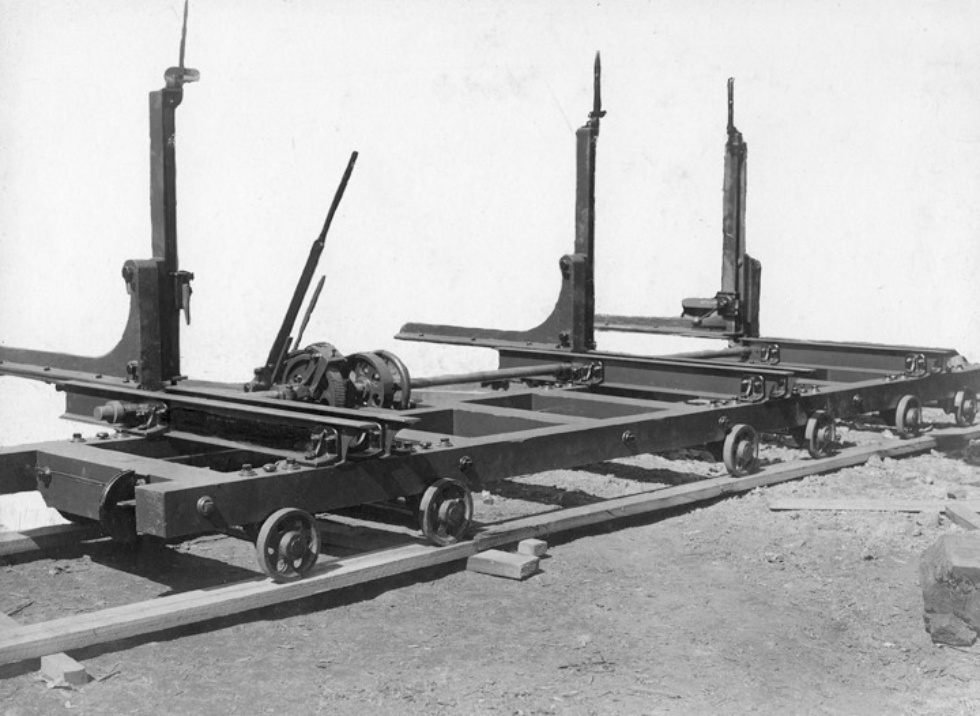
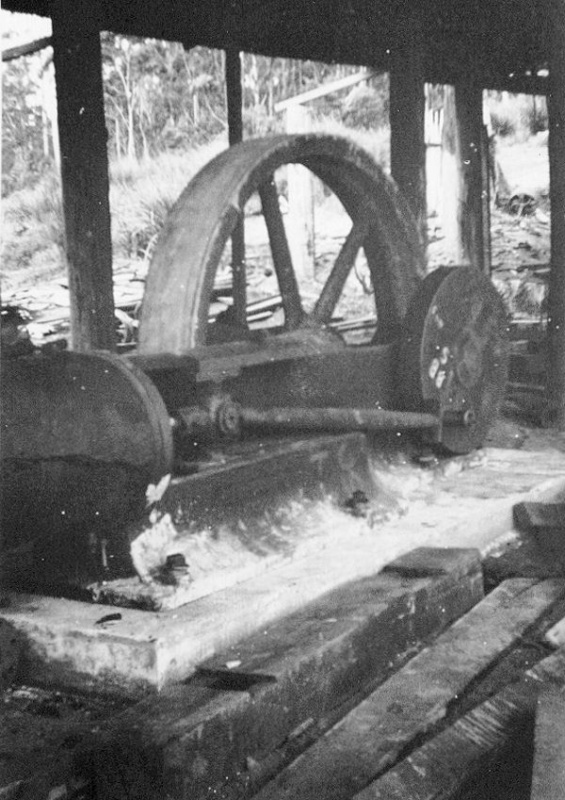
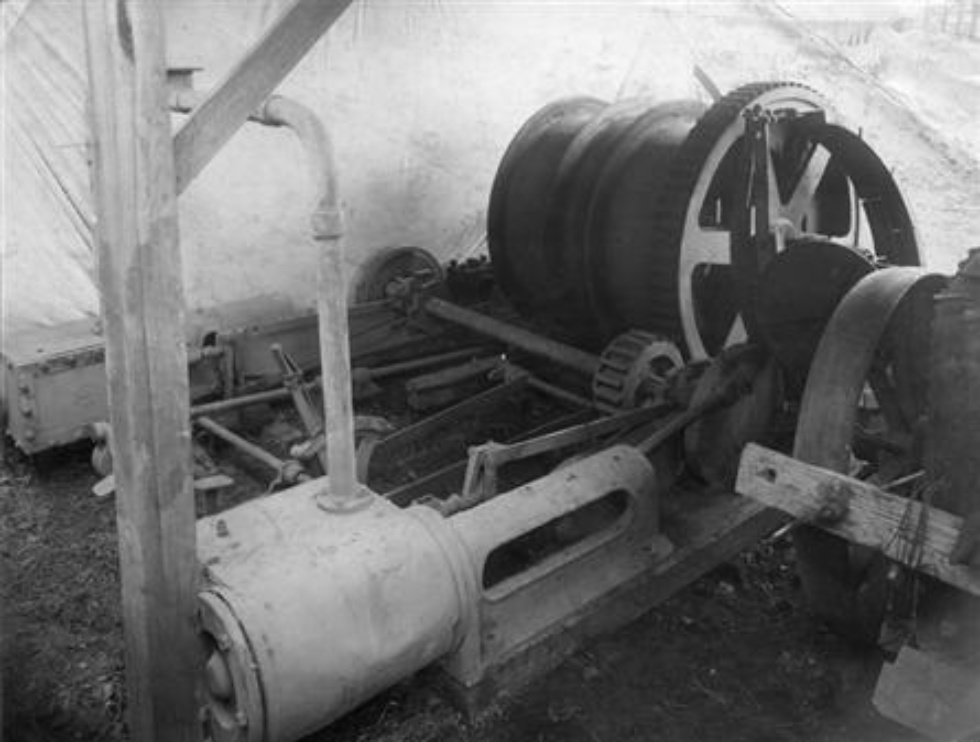
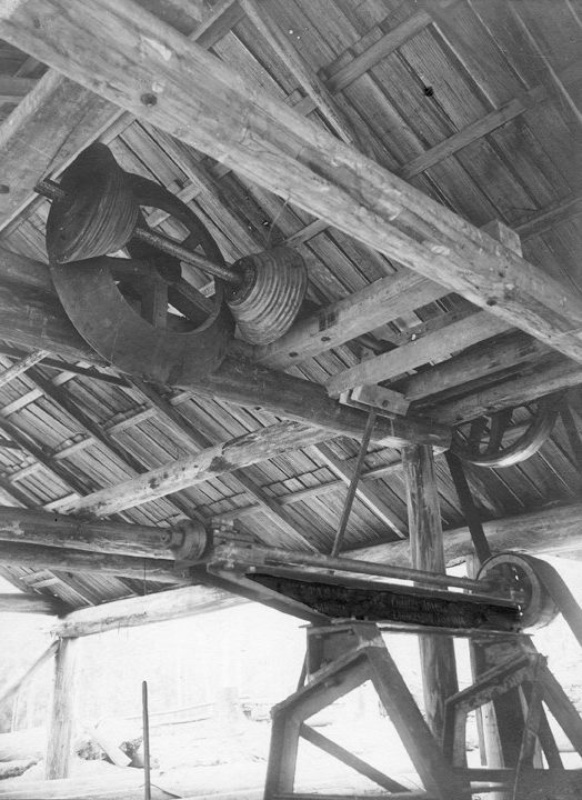
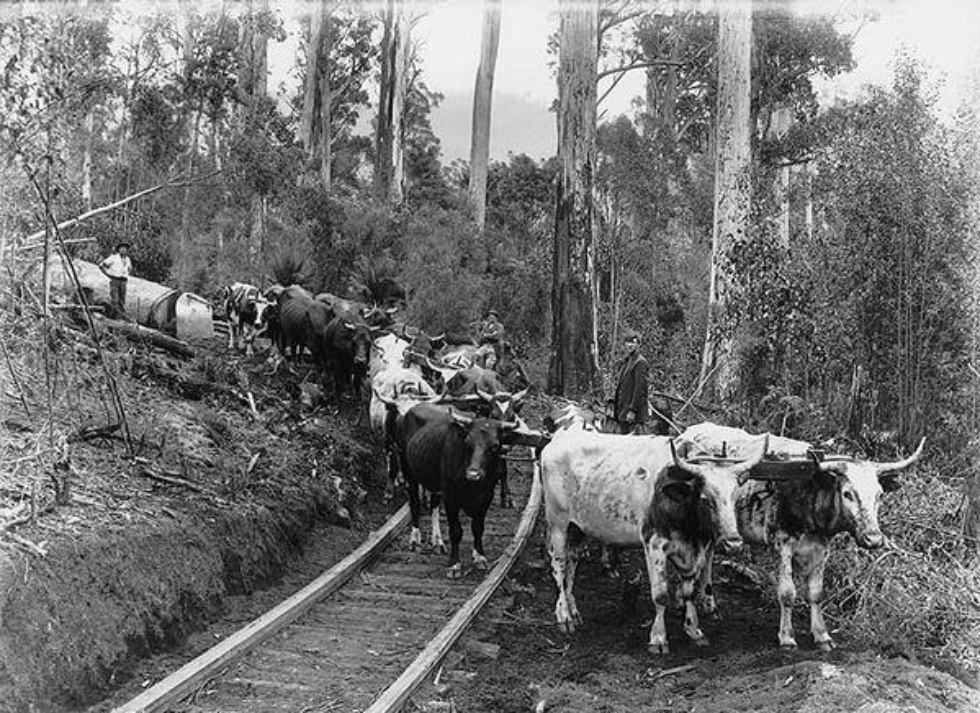
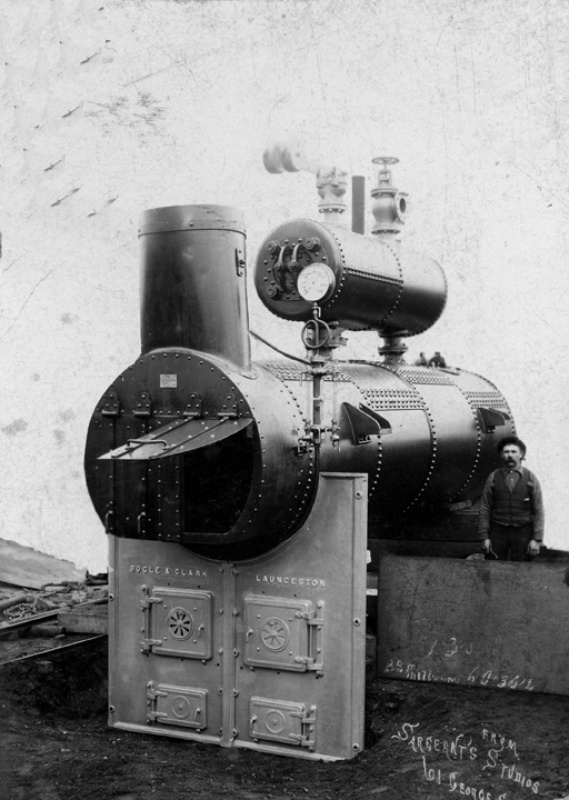
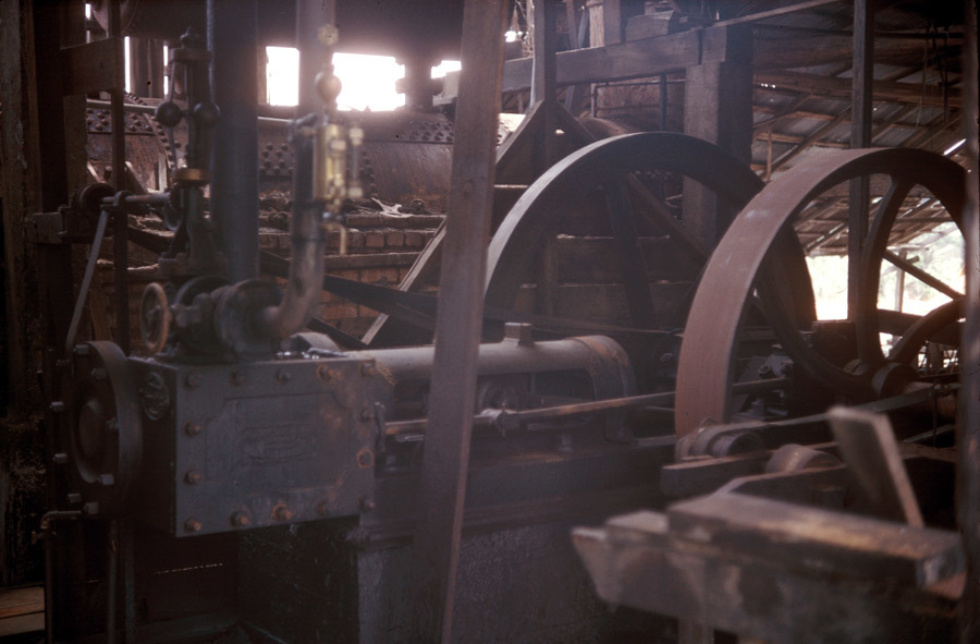
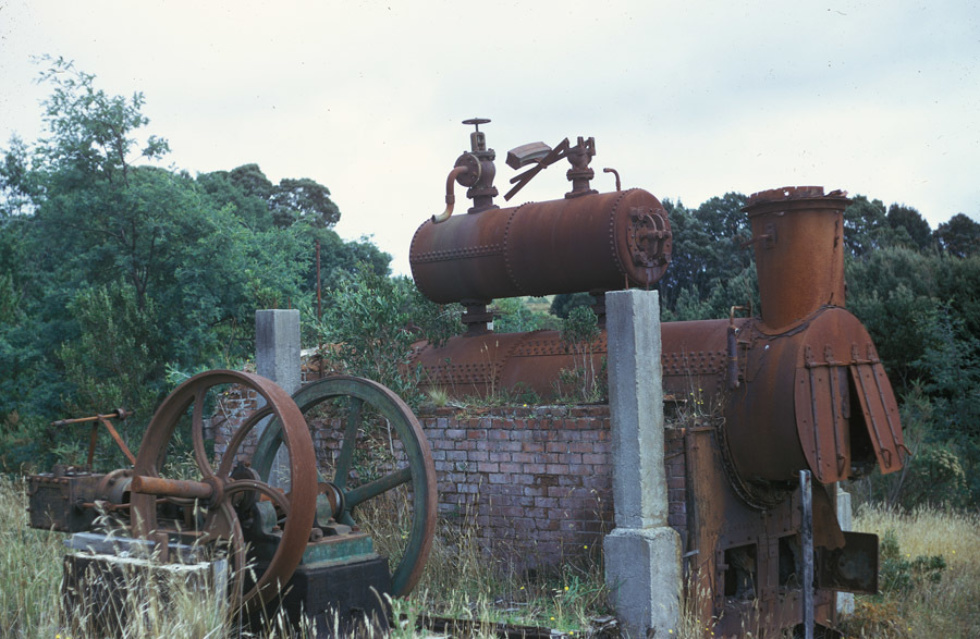