Our History
The Agnew
In 1904, Bogle & Clark tendered for the major refit of the S.S.Agnew The Agnew was a completely equipped steamer built in 1887 by R Kennedy of Hobart, for the operating of a Preistman Grab Dredge. She was to be used for dredging the mouth of the Mersey River at Devonport but due to the exposed situation and the necessity of being moored while dredging proved unsuitable. The work of conversion to a suction hopper dredge was one of considerable magnitude. A new boiler, gravel pump, pumping engines and dredging equipment were all designed by Edwin Bogle and constructed at their William St. works. The pumping engines were marine cross compound high-speed engines with balanced cranks operating at 240 rpm at which speed the indicated horse power was 100. The pump had a suction of 15 inches and a discharge of 16 inches and was specially designed to withstand the abrasion and wear of sand. On her preliminary trails the pumps were found to move 200 cubic yards of sand and shale in an hour and the vessel was capable of performing this in quite a considerable seaway. The conversion of the Agnew was completed in 120 days and a cost of £1820
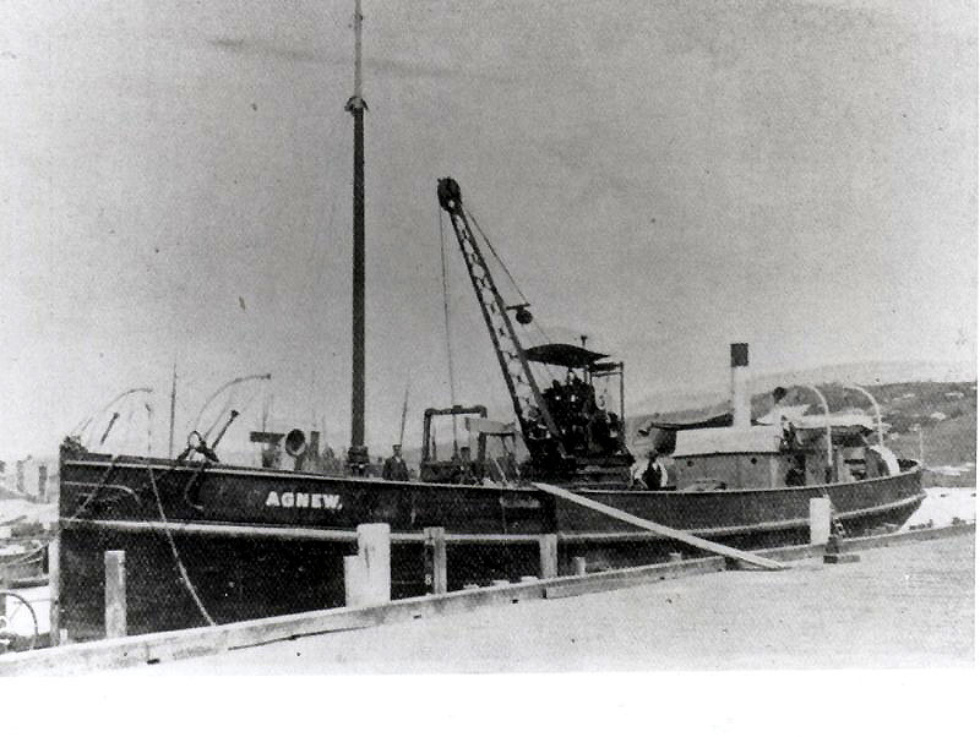
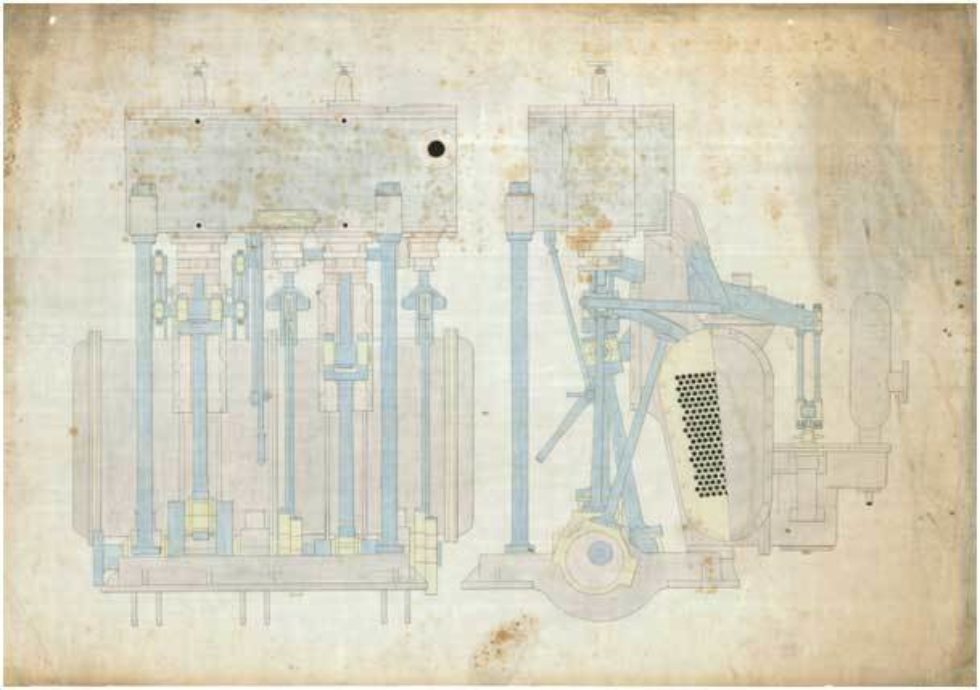
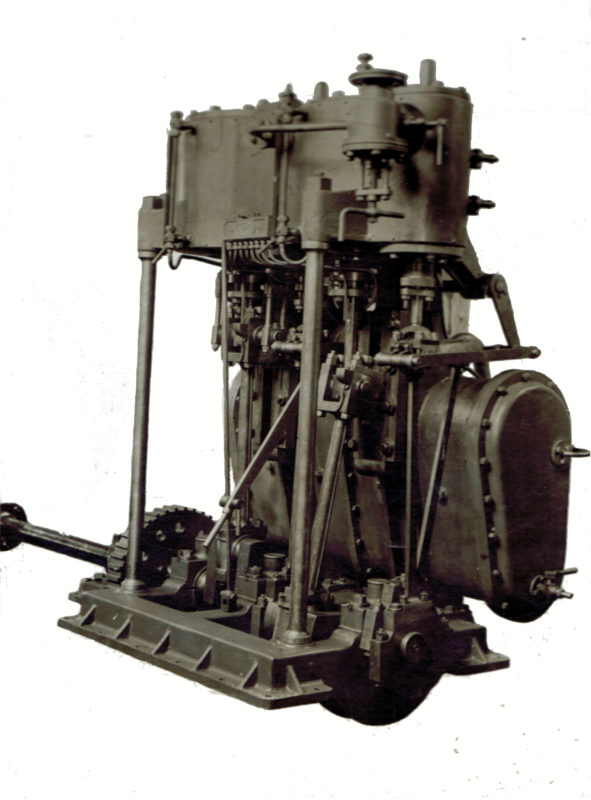
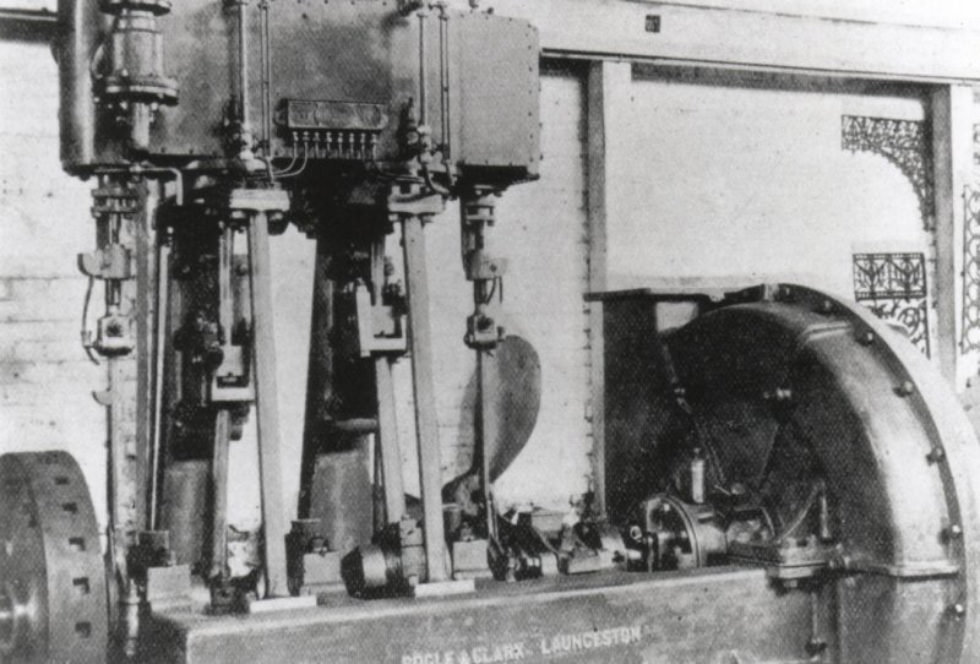
The Agnew being a fully self-contained suction and hopper dredge was working on the mouth of the Mersey River dredging away the sand bar that forms on the outer tip of the break water. Once she had filled the hoppers she went to sea to dump the load of sand and shale in her hold. On her return from one of these excursions in 1937 her skipper misjudged the entrance to the river in a thick fog, and ran her up on the break water. Efforts were made to re-float her, but to no avail. Her equipment was salvaged and she eventually broke up on the rocks, her remains can still be seen today.
An interesting excerpt from the Examiner Wednesday 29 June 1904
The Dredge Agnew.
AN EXTENSIVE ALTERATION.
OFFICIAL TRIAL ON THE RIVER. The dredge Agnew, the property of the Mersey Marine Board, has been at the Launceston wharf for over three months undergoing alterations at the hands of the Glasgow Engineering Company, late Messrs Bogle and Clark. When she arrived the Agnew was a hopper dredge; now she has been converted into a suction pump dredge, and is intended for work on the Mersey bar. The formation of this bar (remarks an article in yesterday's "Telegraph') is of fine hard sand and shingle, which has restricted the draught of water of vessels entering the harbor to 14ft at low water, spring tide. Of recent years considerable improvement has been effected, first by dredging with a ladder dredge, and latterly by the construction of a training wall, so that the ebb flow of the tide helped to create and maintain a channel. The action of the tides, however, was found insufficient to accomplish the result, and dredging operations on the bar had to be resorted to. The dredging of open sea bars presents a set of conditions entirely different from those met with in ordinary river dredging, and a special type of vessel has to be designed to meet the conditions.
Owing to the exposed situation and the consequent necessity of working in considerable seaway, it is impracticable to use anchorages of any kind or to load the material into barges alongside. The type of dredge, therefore, becomes a self-propelling; hopper steamer equipped with a centrifugal pump, which pumps up the sand and shingle from the bar while the vessel is steaming slowly over it. The spoils are received into the hopper in the hold of the vessel, and discharged at sea through doors in the bottom. Mr. Edwin Bogle was consulted in October last year by representatives of the Mersey Marine Board, which resulted in plans being submitted for the con- version of the Agnew into a dredge suit- able for the conditions mentioned. A tender was -submitted by Bogle and Clark, and the work of altering the vessel was entrusted to them.
The Agnew is a completely equipped steamer, and was built in 1887 by Messrs R Kennedy and Sons, of Hobart, for operating a Priest man grab dredge, but owing to the necessity of being moored while dredging, as already pointed out, she proved unsuitable, and was subsequently employed solely as a barge. The work of conversion has been of considerable magnitude, consisting of a new boiler, gravel pump, pumping engines, and dredging equipments, all of which have been built from designs by Mr. Bogle, and constructed at the works of his firm in Launceston. The engines with the pumps are good examples of marine cross compound high speed engines, and all the parts are proportioned with unusual liberality, the object being to construct the very best engine that can be built for the purpose. The cranks are balanced, and the engine runs smoothly and steadily at 240 revolutions, and the indicated horse power is 100. The pump has a suction of 15in and a discharge of 16in, and is specially designed to withstand the abrasion and wear of the sand for a great length of time, and to give freedom of flow through the passages.
The runner is of cast steel, with removable hematite shoes. The pump runner is also entirely encased in a removable hard iron liner. There is a thrust bearing on the shaft of the multiple collar type, and an intercepting pressure chamber provides for the exclusion of the sand from the pump shaft bearing. The boiler is of the marine return flue type, being 9ft in diameter by 9ft long, and built entirely of steel, to the highest class Board of Trade requirements for a working pres- sure of 120 lb to the square inch. This boiler supplies steam to both the propelling and pumping engines. The suction pipe enters over the side of the boat. There is a heavy flanged socket casting fitted on to a sliding carriage, which receives the swivel elbows of the suction pipe. The elbow is a steel casting, and has sufficient bearing in the socket to take the entire strain of the suction pipe without any additional support. The swivel also permits of a free action of the suction pipe, both vertical and athwart slips when working in a seaway. The suction pipe is 40ft long and made of wrought steel-welded tubing, and the drag is cowl-shaped, the opening to which is provided with a grating to prevent the passage to the pump of material of a size to endanger a choke. From the pumps the discharge is carried forward into two large troughs, which have openings or valves at suitable intervals, so that the material can be properly distributed in the hoppers. The discharge to the hoppers consists of a mixture of sand and water, the percentage varying from 10 to 40 per cent, according to circumstances. The water flows over the combings and passes over the deck into the sea, while the sand precipitates in the hoppers. The capacity of the pump is 200 cubic yards per hour; actually, however, a consider able percentage of sand goes overboard with the overflow, especially if the sand is light and slow to precipitate.
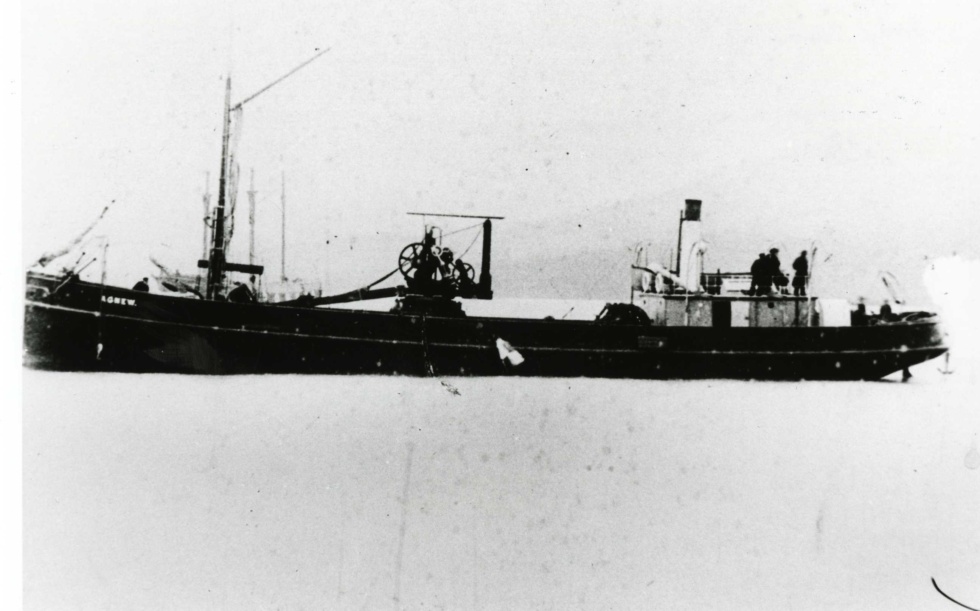
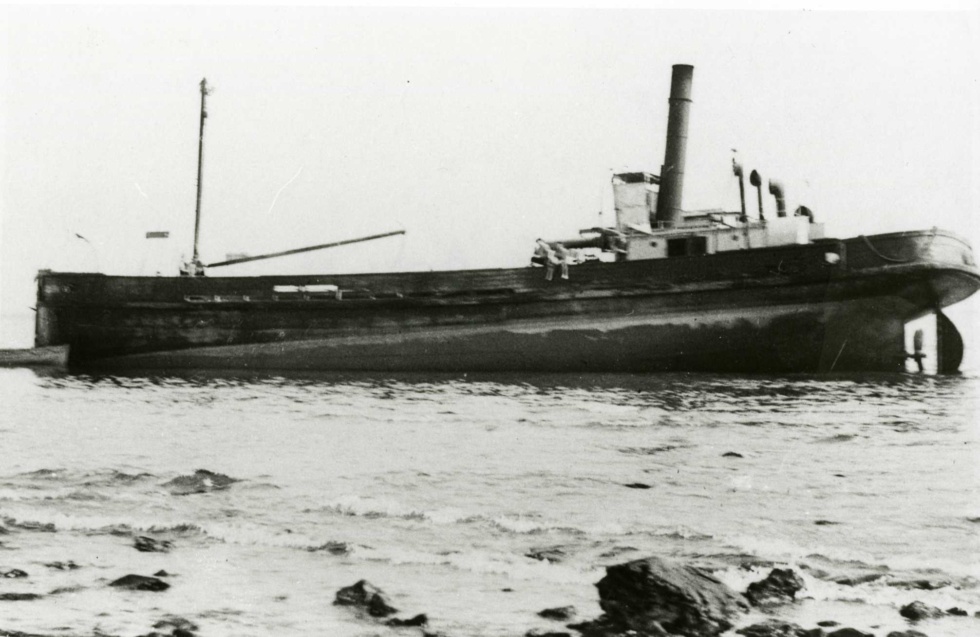
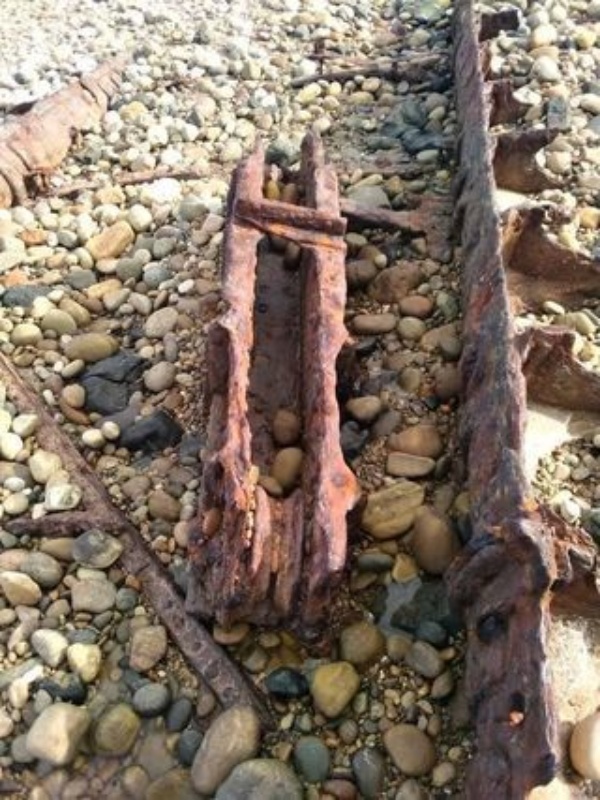
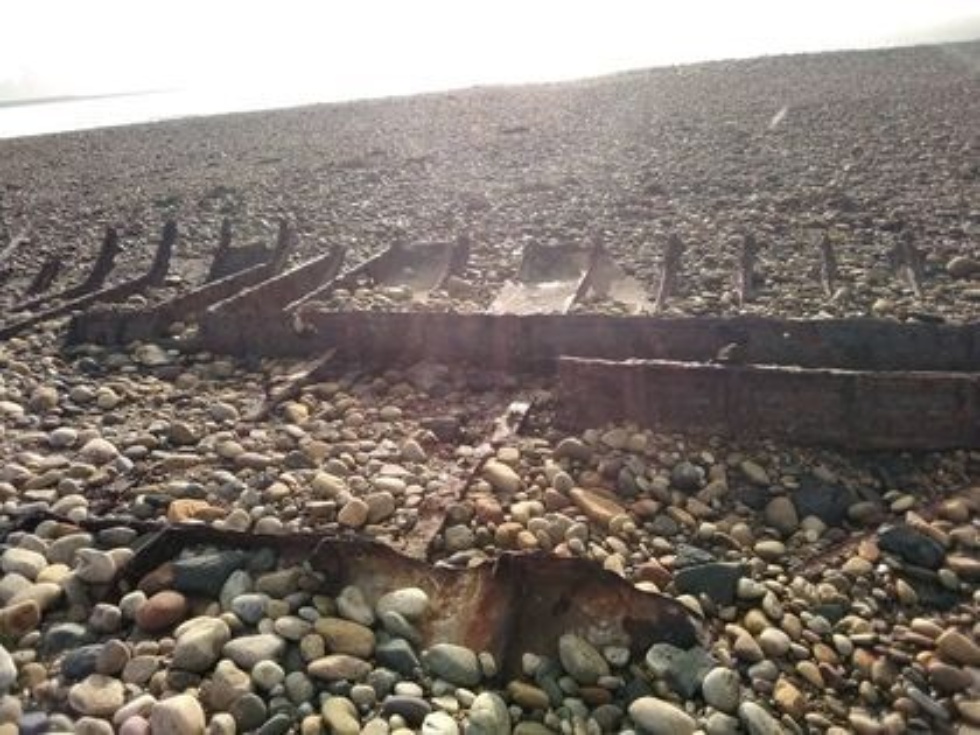